稳定器简介:
Stabilisers: The PVC molecule is unstable to heat and light. Heating PVC causes breakage of the Polymer chains, liberating Hydrochloric Acid gas. The HCl catalyses more degradation and the degradation can become explosive, releasing large quantities of corrosive HCl and other toxic gases. Exposure to Ultraviolet Radiation also breaks up Polymer chains but is much slower than Heat degradation.
Heat Stabilisers: To process PVC, it has to be stabilised against the action of Heat required at processing temperatures. Most Stabilisers contain metal elements which react with HCl and inhibit further degradation. They are Metal Salts, Soaps or Complexes. Stabilisation of PVC is a vast subject, and they are the second most important ingredient in UPVC Formulations and after Plasticisers in a Flexible PVC formulation. Some of the most important families are:
|
Type |
Form |
PHR used |
Clarity |
毒性 |
Odour |
Cost/Kg |
铅 |
粉末 |
2 -4 |
Opaque |
Toxic |
None |
〜120-150 |
ba- cd |
Liquid |
1.5 - 2.5 |
Clear |
Very Toxic |
Slight |
~ Rs 200 |
Ba - Zn |
Liquid |
2 - 3 |
Clear |
Toxic |
Slight |
~ Rs 190 |
Cd - Zn |
Liquid |
2 - 3 |
Clear |
Toxic |
Slight |
〜Rs 220 |
Ca - Zn |
Liquid |
3 -4 |
Clear |
Non-Toxic |
Negl. |
〜250卢比 |
罐头 |
Liquid |
0.5 -1 |
Crystal |
T & Non |
强的 |
〜350卢比 |
Ba - Zn |
Liquid |
2 - 3 |
Clear |
Toxic |
Slight |
~ Rs 190 |
最好选择目标应用程序的稳定器选择,最好与PVC树脂供应商的稳定剂供应商和技术服务单元进行协商,但是,作为指南,下表将是有用的。
Stabiliser application areas:
Type |
热稳定性 |
Main Applications |
Not recommended for |
铅 |
Very Good, esp. long term. |
电缆,管道和配件,袖子,轮廓。最便宜。 |
清除申请。可能是有毒的。 |
罐头 |
最好的 |
透明管和板,高质量管,医疗 |
引起用铅染色的硫化物染色。最昂贵的稳定器。 |
Cd - Zn |
Moderate |
ROHS Cables, Non-Toxic. Pipes and Extrusions. |
对于高热量历史。 |
ba- cd |
Good |
Leather Cloth, Calendared products, Footwear. |
无毒应用 |
Cd - Zn |
Moderate |
Foamed Leather Cloth |
对于高热量历史。 |
金属锻炼 |
Low |
润滑作用的联合稳定器 |
Sole Stabiliser. |
Newer families of heat Stabilisers are being offered with the background of Heavy Metal environments contamination concerns. Organic Stabilisers and Calcium Zincs are in the forefront of this trend.
Because of its relatively lower cost and strong Stabilisation action, Lead stabilisers have historically been the most popular
• Lead Stabilisers: The common Lead Stabilisers are:
o tbls- tri碱性铅硫酸盐。强大的热稳定剂,因为它具有大约80%的PBO,这是吸收和中和HCl的活性成分,然后在加热时释放。它是无润滑的,不透明的,不能用于透明/易位应用中
o dbls-二元铅硬脂酸酯。润滑稳定剂对于在挤出机的混合和计量区润滑非常有用。半透明。
o LS- Lead Stearate. Weakest Lead stabiliser. Strong external lubricant especially in the early extrusion stages. Translucent.
o There are other Lead stabilisers like Dibasic Lead Phosphite, used when Light Stability is important and Dibasic Lead Phthalate, used for high speed extrusions, but these are not being covered in this article, as they have niche usage.
Calcium Stearate and Stearic acid are often used along with Lead stabilisers primarily to balance the Lubrication. CS is a weak stabiliser but an excellent internal lubricant, very effective in late stage lubrication at barrel discharge and die head. Stearic acid is a strong external lubricant, Excessive use can lead to screw slippage and poor gelation.
Lead Content of Lead Stabilisers.
铅稳定系统具有的一个缺点是,良好,平衡的配方需要所有铅稳定剂以及硬脂酸钙和更多润滑剂的组合。其他系统(例如罐头和混合金属)通常是一级稳定剂和一两个润滑剂。使用线索,可能需要仔细称重六到七种成分,这需要熟练的操作。
Lubricating Lead Based One Pack Systems
The Stabiliser mix for the high-volume PVC Pressure Pipes which I have used extensively in the past till the one packs came on the scene, is given in my article on Volume Costs, referred to in Page 6.
您将注意到,t的推荐剂量he regular grades of one packs for PVC Pipes offered by leading manufacturers start at about 2.2 to 2.4 PHR. This matches up with the dose of 5-6 ingredients above and is the basis of the convenient one pack systems.
The initial one packs offered were premixed single component stabilisers. The desired quantity was weighed out into packets according to the amount of Resin charged per batch. This is in line with the practice followed inhouse, but separate weighing of 5-6 ingredients was prone to weighing inaccuracies, especially of the minor ingredients. The stabiliser manufacturers used to mix the one pack recipes in bulk, and the mix was then meter measured and packed in easy to use packets, say for 25 kgs. PVC, 50 kgs, etc.
在八十年代初期,对这个概念有很大的抵抗。我的个人经验是,在Shriram and Prc(DCW)中使用单个稳定器制定了近十年之久,当我去科威特时,我被介绍了一个包装系统的便利性。Baerlocher GmbH的一包吸引了人们的大开眼界,当我1978年回到印度并加入Waldies时,我想在印度介绍这一概念,并加入了著名的铅氧化物和PVC稳定器公司Waldies。
At that time, PVC Pipe markets was starting to grow rapidly with the leaders like Wavin, Finolex, Garware and Chemplast using large capacity imported extruders, while most the others were equipped with the venerable Windsor RC-100. Remember, at that time, PVC Pipes of the popular sizes up to 110 mm were reserved for small scale, and only the RC-100 (meaning 100 lbs/hr, about 40 kgs/hr) could be afforded by many who were entering the field as small-scale industries.
At that time, the PVC recipes for pipes were a closely guarded secret, controlled by the plant technical heads. Much to the dismay of my friend Mr. Anil Anand of ALA and myself, who were trying to push the one pack concept, we found that the technical chiefs were not at all interested in switching to the ease of a preformulated one pack. It would seriously reduce their importance in their companies!!
There was another factor working against the type of efficient one pack systems available abroad in the early eighties. The RC-100s with their co-rotating screws and low outputs and high residence times, required higher dosages, sometimes 4-5 PHR and had to be formulated like single screw extruders recipes. As the PVC pipe industry had started with small diameter conduits, many single screw extruders were pressed into service for water pipe. Even Chemplast were using large single screw extruders as per their American processing DNA. Added to the higher stabilisation costs, expensive flow promoters were needed for single screw pipes to match the strength of pipes made on the new imported Counter Rotating twin screw extruders.
The industry rapidly shifted to the imported Twin Screw extruders from companies like Cincinnati and Kraus Maffei, Battenfeld etc., and as the Pipe market was booming because of the WHO funded drinking water projects. The extruders were actually airlifted, such was the demand. Later in the 80s and early nineties, with more number of modern high output extruders being the norm, the one pack concept started taking hold.
The next step from premixed powders was to safer handling, non-dusting forms. One big drawback with handling Lead Stabilisers in the factory is susceptibility to lead poisoning of workmen, if handling, housekeeping and dusting was not kept under control. Newer one pack delivery systems were developed by heating the mix to about 160C so that the Lubricants, Calcium Stearate, Lead Stearate and Dibasic Lead Stearate melted and formed a dough with the non-melting TBLS. The dough was then extruded into pellets or pressed and chipped into flakes. This form was much safer to handle and gradually found acceptance.
This has been further refined by Stabiliser manufactures who start with Litharge (PbO). They react this with carefully prepared proportions of Sulfuric Acid, Stearic acid and some other lubricants like Calcium Stearate and special waxes. On completion of the reaction, all the PbO is converted to TBLS, DBLS and LS as per the formulation proportions. The reactor discharges to a rotating drum, where the paste is cooled and flaked off.
Non-lubricating One packs leads do没有足够的润滑剂来涂上混合物中的所有固体,并作为粉末出售。它们被广泛用于电缆和电线,轮廓,刚性和柔性的雪橇,注射模压配件等的应用。
Special applications like PVC Window Profiles and Injection moulded fittings need some more ingredients other than Stabilisers and lubricants like Impact Modifiers and Flow promoters.
Window profiles require 3.5-5PHR impact modifier and 1.5-2PHR Flow Promoter. When this is sold as a package in a one pack, the dosage must go up by 5-7PHR, that is 2.4+5=7.4 and 2.4+7= 9.4PHR. The price of the one pack goes up as the additives are quite costly.
In Injection moulded fitting, which are processed on single screw extruders, a flow promoter needs to be added. At 1.5PHR addition, the One pack dose goes up to 4PHR. Again, the one pack will be costlier than the normal pipe one packs.
如果需要,也可以提供一个包装,例如抗紫外线,抗氧化剂等。One Pack制造商投入了很多投资,用于开发适合应用的合适润滑剂混合物,并为PVC管道的同一应用提供多个等级,例如正常,填充,高度填充,单个或双螺钉等。可以提供。一包的价格会随选择的特殊成分而变化。
剂量和定价
在竞争非常激烈的领域,PVC管,where the demand is for cheaper and cheaper inputs, CaCO3 fillers get added to the one pack to drop the price, However, to maintain the same stabilising efficiency, the one pack PHR has to be increased by the amount of inert filler added. This if 1 kg extra of filler is added, no doubt the price will go down, but the dosage goes up by 2.4+1=3.4. As most processors clamouring for cheaper one packs are making highly filled pipes, the one pack must be further boosted to maintain the same % of active PbO as in standard formulations.
The implications of adding fillers to cheapen One packs must be clearly understood, as Per Kg cost reduction is not the only factor.
Here are some examples:
In this example, I have started with a standard PVC Pipe one pack. If an economical filler containing One pack is used, the starting point will be 3.2 PHR instead of 2.4PHR, and by the time filler loading reaches 100 PHR, the loading must be nearly doubled for trouble free operation. A common mistake by processors is to stick to the same PHR used in BIS Pipes as they increase filler. This drops the active PbO content and lubrication balance and can lead to severe processing problems.
必须通过将每公斤一包成本乘以一包成本以及PHR所需的增加水平来进行研究,以达到每100 phr树脂的稳定成本,以确定其降低成本的有效性。
填充物的添加量,尤其是在较高剂量下会降低成本。但是重要的是,标准或经济的一包稳定成本是否较低。
Another factor which is important is the volume cost, for which the density of each ingredient is crucial. Anything added with a density more than PVC will increase the density (Like One Packs, Fillers, TiO2)
For accurate density calculations and assessment, the actual density of all the ingredients must be known. The one pack density is important as this figure is not usually given in Technical Data sheets.
For further clarity on the effect of Density and filler loading, please refer to my article
//www.esper-magazine.com/plastic-technical-articles/volume-cost-and-ismportance-in-plastic-applications/1561
Calcium Zinc One Packs.
With the world moving away from Lead stabilisers. Calcium Zinc systems are becoming prominent for manufacturing Lead Free Pipes and where ROHS requirements are to be met.
Calcium Stearate is the most common non-Lead stabiliser. However, its stabilising power is quite low and is more viewed as a very effective Internal Lubricant, playing a major role in Lubrication at the die head for smooth extrusion and finish.
Calcium Soaps have been combined with Zinc compounds and the resultant Calcium Zinc Stabilisers have steadily improved in stabilisation efficiency. Driven by the intensive R&D of the stabiliser industry, Calcium Zincs are rivalling Leads in dosages, 3PHR vs 2.4PHR.
The lubrication systems are quite complex in Calcium Zinc systems for boosting the efficiency, so many of the Calcium Zinc grades are available as one packs and not individual components.
The other major Stabilisation system is with Tins, very popular in the Americas, as they were very effective with single screw extruders, which was the norm there before the Americas also switched over to Twin screw.
Tin Stabilisers like, the Mercaptide family, are all liquids. This does not make it conducive for a one pack delivery system. Normally Tin Stabilised pipes are made with single components, with the lubricant balance being critical for excellent performance. Tin stabilisers are more expensive than Leads, but as they are so efficient, processers with top of the line extruders are reported to have come down to 0.3-0.5 PHR with the powerful methyl tins and being competitive to lead systems.
There are many suppliers of One pack systems, whose numbers have increased as one packs are now universally used by the huge PVC Pipes and Profiles sector
悉达多·罗伊(Siddhartha Roy) |
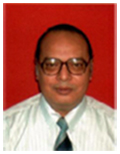 |
Mr. Siddhartha Royis a Chemical Engineer from IIT Kharagpur (1968). He has worked with plastics all throughout his career. He was actively involved in development of PVC markets and applications, especially Pipes and Fittings. He worked with Shriram Vinyls, PRC (now DCW) and Chemplast, manufacturers of PVC Resin & Compounds. He has managed a PVC Pipes & Fittings factory in Kuwait and helped Jain Pipes (now Jain Irrigation) set up their Pipe production facilities.
He headed R&D at VIP Industries, Nasik, and is well versed in the processing of Polyolefins, Styrenics, Polyamides and PC. He has been active in IPI activities and has delivered several Endowment lectures. He was recently awarded the Fellowship by the Governing council of IPI for his contribution to the Plastic Industry. |
|
Previous Article
Next Article
{{comment.DateTimeStampDisplay}}
{{comment.Comments}}